Ahorro y eficiencia energética en la industria y el proceso de recuperación de disolvente
SECTOR
LA BÚSQUEDA CONTINUA DE LA MAXIMIZACIÓN DE LA EFICIENCIA ENERGÉTICA, APLICADA TAMBIÉN A LOS PROCESOS DE DEPURACIÓN DE LAS EMISIONES ATMOSFÉRICAS QUE CONTIENEN COV, HA LLEVADO A LA IDENTIFICACIÓN DE UNA TECNOLOGÍA QUE PERMITE REDUCIR EN MÁS DE UN 30 % LA CANTIDAD DE VAPOR UTILIZADA EN LAS INSTALACIONES DE RECUPERACIÓN DE DISOLVENTES.
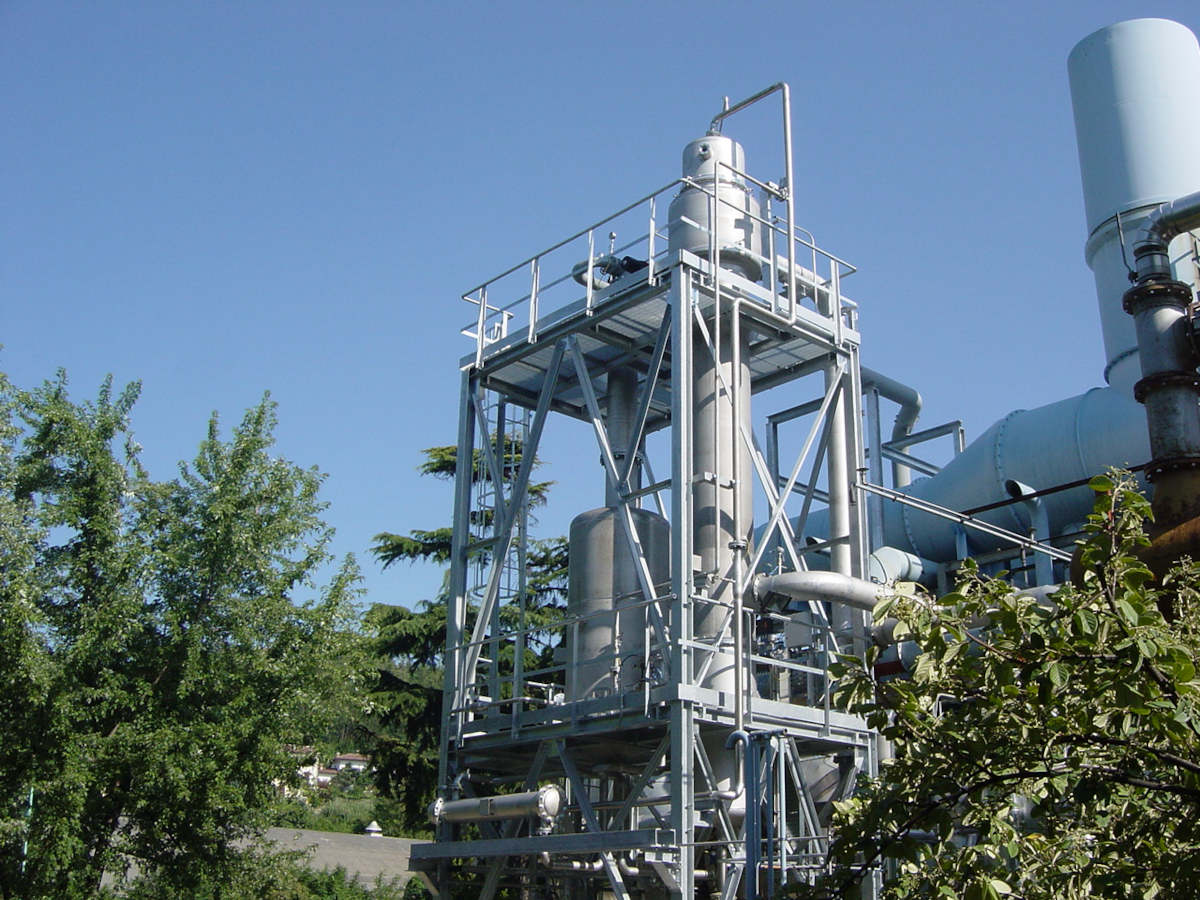
EL FUNCIONAMIENTO Y EL IMPACTO ENERGÉTICO DE LOS PROCESOS DE RECUPERACIÓN DE DISOLVENTES CON CARBONES ACTIVADOS
Las instalaciones de recuperación de disolventes con carbón activado permiten atrapar los disolventes contenidos en las emisiones atmosféricas mediante la adsorción en los carbones activados.
Para permitir la recuperación posterior, los disolventes se eliminan del carbón activado, utilizando un fluido caliente que, en el caso de los disolventes insolubles en agua (tolueno, hexano, benceno) es vapor.
El fluido caliente y el disolvente eliminado en la fase gaseosa de los carbones activados se condensan y enfrían posteriormente y se separan por gravedad.
El principal consumo de energía de este proceso está relacionado con el uso de vapor, que luego debe condensarse.
El disolvente se recupera en el proceso de producción, mientras que el agua condensada puede reutilizarse para producir vapor de nuevo.
OBJETIVOS DE EFICIENCIA ENERGÉTICA Y MEDIOAMBIENTAL
El objetivo es optimizar el proceso de recuperación de disolventes no solo en términos de cantidad, sino también en términos de eficiencia del proceso de recuperación, reduciendo así la necesidad de energía, optimizando los recursos utilizados y minimizando los residuos producidos.
LA SOLUCIÓN A TRAVÉS DEL PROCESO DE RECUPERACIÓN DE ENERGÍA
Es posible reducir el consumo de vapor utilizado en cada regeneración de los carbones activados aprovechando el calor latente aún presente en la mezcla disolvente-vapor (desorbato) que sale del adsorbedor durante la fase de regeneración. En los primeros minutos, el vapor se condensa por completo, ya que todo el calor se cede para calentar el adsorbedor y el carbón; después, el vapor (que solo actúa como medio de transporte) sigue estando disponible en forma de vapor que sale del adsorbedor.
Gracias al ligero vacío producido por un termocompresor (alimentado con vapor fresco a 8-9 bar) y al calor proporcionado por el desorbato, es posible producir vapor reevaporando el condensado previamente acumulado. El vapor así producido, mezclado con el vapor fresco de alimentación al termocompresor, constituye el caudal de vapor necesario para la regeneración del carbón activado.
Con este sistema, el suministro de unos 0,7 kg de vapor fresco a 8 bares generado con calderas convencionales produce alrededor de 1 kg de vapor recuperado en vacío (97 °C) para un total de 1,7 kg de vapor apto para la regeneración (la cantidad de vapor fresco suministrado en esta fase es, por tanto, solo el 41 % de la necesaria para un sistema convencional).
Dado que la recuperación de energía no es posible en la primera fase de regeneración, que dura aproximadamente un tercio del tiempo total de regeneración, la reducción del consumo total de vapor es de alrededor del 30 % del consumo total.
LOS RESULTADOS OBTENIDOS
- Reducción del consumo de vapor > 30 %, con la correspondiente reducción de las emisiones de CO2
- Posibilidad de obtener certificados de eficiencia energética
- Mejora de las condiciones ambientales: Menor consumo de agua de enfriamiento requerido para la condensación del disolvente y menos condensado por tratar
- Reducción del consumo de agua de alimentación de la caldera y de los reactivos necesarios para su pretratamiento.
- Reducción del consumo de energía relacionado con la reducción de la carga térmica a la torreevaporativa: reducción del consumo eléctrico para asegurar la circulación del caudal de agua de enfriamiento y el consumo eléctrico de los ventiladores de la torre.
VENTAJAS DEL SISTEMA
El sistema es adaptable a cualquier instalación existente.